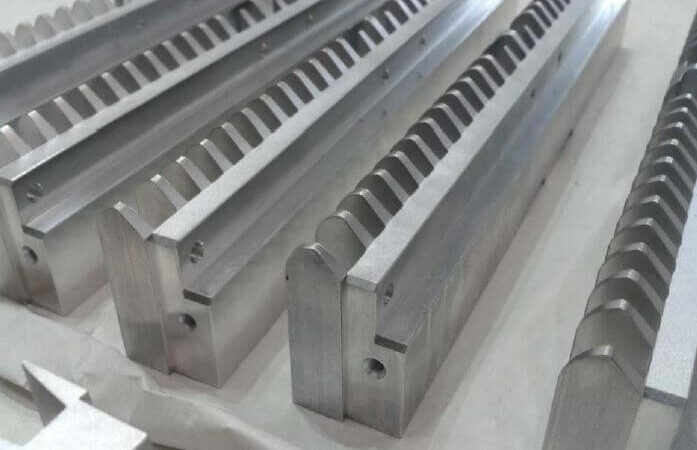
When manufacturing metal parts, selecting the right process is essential to balance strength, complexity, cost, and performance. Three primary methods—extrusion, casting, and forging—each offer unique benefits and limitations. Here’s a breakdown to help engineers choose the best solution for their needs.
- Process: A metal billet is forced through a die to form specific cross-sections.
- Advantages:
- Produces a wide variety of shapes with enhanced mechanical strength from an elongated grain structure.
- Lower tooling costs and ideal for high-volume production.
- Disadvantages:
- Limited to 2D shapes, with potential surface defects like oxidation or cracking.
- Lower stiffness compared to forging.
- Best For: Simple shapes or high-volume projects where strength isn’t the top priority.
Casting
- Process: Molten metal is poured into a mold to create complex shapes.
- Advantages:
- Excels at producing intricate geometries and large parts, including no size limit in sand casting.
- Can be cost-effective depending on the application.
- Disadvantages:
- Lower strength than forged parts, with risks of internal defects like porosity or surface voids.
- Often requires additional machining for a quality finish.
- Best For: Large or complex parts where cost matters more than maximum strength.
Forging
- Process: Solid metal is compressed under extreme force into high-strength parts.
- Advantages:
- Superior strength and structural integrity due to a refined grain structure.
- Ideal for stress- and shock-resistant components (e.g., pistons, gears).
- Closed-die forging supports complex 3D geometries, tight tolerances, and eliminates defects like porosity.
- Offers a high-quality finish.
- Disadvantages:
- Higher costs, especially for intricate designs or smaller runs.
- Best For: High-performance, durable parts with complex shapes.
Key Considerations for Engineers
- Need strength and 3D complexity? Choose forging, especially closed-die forging, for top-tier durability and precision.
- Prioritizing cost and volume? Extrusion suits simpler, high-volume designs.
- Complex but less critical parts? Casting handles large or intricate shapes economically.
Our Expertise in Closed-Die Forging
At PA in China, we specialize in die forging, crafting high-quality aluminum parts for medical, automotive, and renewable energy industries. Leveraging advanced 3D technology, heat treatment for added strength, and multiple options for finishing process, we deliver precision and durability from ounces to over 25 pounds. With 25+ years of experience, our diverse clients trust us to collaborate on their most complex designs, providing creative, reliable solutions.